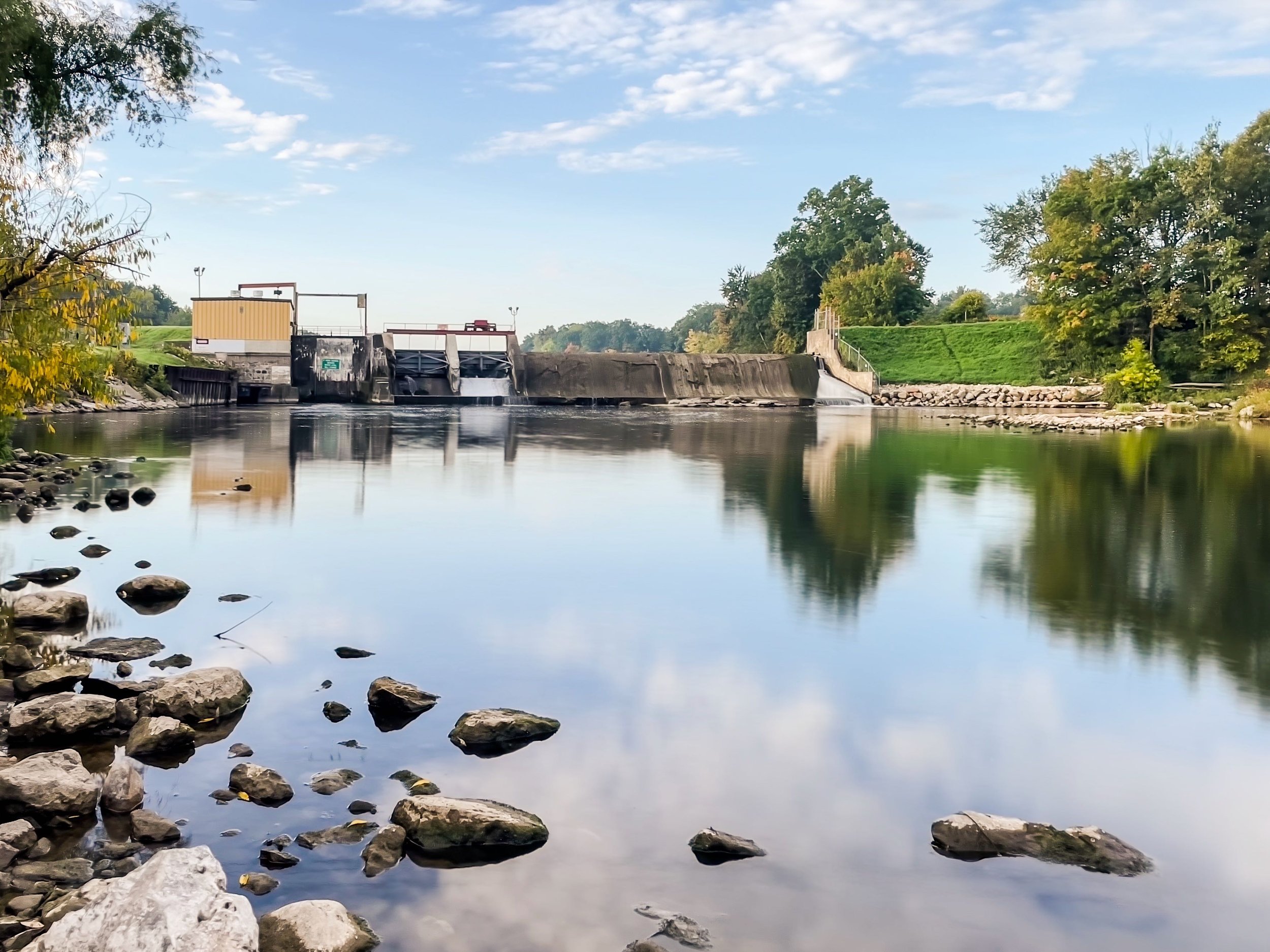
Bringing Power to the People
Modernizing Hydroelectric Facilities
It's a fact: the average hydroelectric facility has been in operation for over six decades. In the United States, the 50 oldest electricity-generating facilities are all hydroelectric, with the newest dating back to 1908. A tour of your average small-scale hydro plant will reveal decades of patchwork repairs and maintenance, a testament to the dedication of generations of staff. But the sad reality of this is that in most plants today, we have WW1 era equipment with antique metering patched in with Disco era sensors to PLCs that predate Ethernet, much less the Internet.
Most operators spend their working days just hoping that it all holds together one more year because nobody can fix half the stuff in there. Documentation (if it exists at all) is often sketchy, literally hand-drawn sketches and notes from maintenance staff who tried to figure it out over the years and left treasure maps of clues hidden in the equipment cabinets. The typical system is so old that you can’t even get the software to connect to it anymore. And the one guy who built it and really understands everything... well he retired years ago and the last we knew he moved to Arizona.
The Challenge for Small Operators
These small operators are often balancing on a razor-thin margin. They find themselves in a precarious position: in desperate need of efficiency upgrades and automation, but historically ill-equipped to bear the monumental costs associated with these enhancements.
This is the paradox of being a small power plant operator. The improvement in automation can empower the operators with real time data logging and database level management of the entire facility. By building a control algorithm based on their specific flow and throughput, weather conditions, and setpoints, we can build a predictive model to ensure that the entire plant is running at peak efficiency matched to the water levels at that moment. Properly implemented this results in a substantial increase in efficiency (and revenue) over antiquated control systems.
Longcastle: Your Solution Provider
Breaking Free from the Past
Traditionally, the industrial automation sector has operated under a closed-source model. Big corporations poured vast sums into designing and developing proprietary PLC hardware and crafting complex, inscrutable software. These systems were a closely guarded secret, accessible only to a select few. High-priced licenses and formidable marketing campaigns ensured their dominance, limiting competition.
A Better Way to Operate
At Longcastle, we believe there's a better way to do business and run a power plant. Would you purchase a truck with the hood welded shut? We think not. We champion the idea that you should have the right to maintain and repair your own equipment. We firmly believe that form should follow function, allowing you to adapt your hardware as your facility and technology evolve. The system should be built to outlast the people who installed it. It should be built in a way that technicians generations from now can easily access, understand, upgrade, and repair it for the future.
The Power of Choice
Our approach gives you the freedom of choice. You can opt to build the entire system from the ground up with our guidance, or you can enlist our services for a complete turnkey installation tailor-made for your facility. You also have the flexibility to mix and match, with you and your team handling certain aspects while leaving others to us. The choice is entirely yours, and we're here to support you every step of the way.
Contact us.
Every facility is unique and presents new challenges in design and problems to solve. While our systems are modular in design, every installation is custom made to fit your systems. If you’d like to book a free consultation with one of our design staff, please fill out this form and you can expect to hear from us presently. We’d love to hear from you and see what we can do to help bring your power plant into the 21st century.